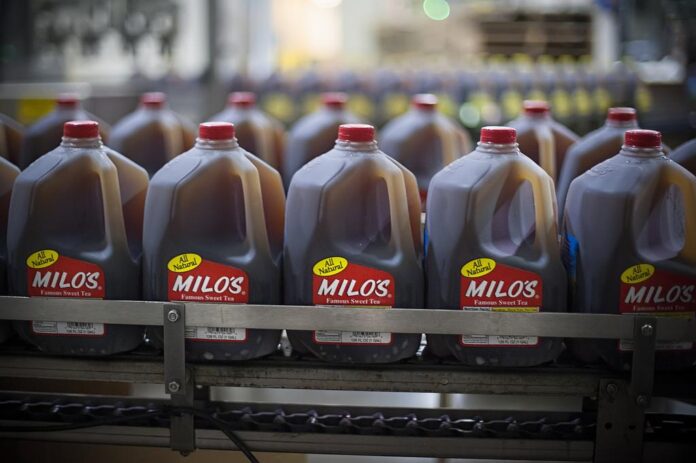
Milo’s Tea Company Deploys Smart Manufacturing to Improve Productivity and Support Expansion into New Markets
Background
Sweet tea, like fried chicken and barbecue, holds a prominent place in its fans’ hearts. For Milo’s Tea, a family-owned company established in 1946, the goal has always been to consistently create and deliver a product evocative of southern charm, comfort, and nostalgia. As such, the company has grown into a nationally recognized whose sweet tea is consistently the number one selling tea product in the US.
As they met success, the team at Milo’s Tea realized their current production facility couldn’t handle the increased demand. Production, which had traditionally operated with two shifts a day, five days a week, had begun running 24/7. However, this wasn’t enough to meet the rapidly increasing market demand. Performance roadblocks, siloed systems, and lack of real-time production visibility made it challenging to identify the best path forward.
Initially, the team thought they needed another production facility to keep up. But then they asked a question which changed everything: “How do we get the most out of our existing assets?” Could reducing downtime and short stops, eliminating waste, and digitizing paper-based records help them substantially achieve their goal of production optimization? Looking to answer those questions, the Milo’s Tea team reached out to Parsec Certified Partner, Polytron.
Polytron’s initial assessment and discovery period helped architect the goals for the project. Establishing a unified system for actionable real-time data, e-records, notes, and journals would be essential for empowering Milo’s Tea. Polytron needed a platform that would enable real-time, data-based decision making, interdepartmental communication, and extensibility—one that would adapt to the continued growth of the company. To enable all of these results and more, Polytron utilized the extensible, agile, multi-site capable MOM platform, TrakSYS.
Overview
To support the growth occurring at Milo’s Tea Company, Polytron implemented the modular manufacturing operations management (MOM) platform, TrakSYS, in a phased approach. Implemented over a two-year period, the phases included solutions for Performance Management (OEE & Downtime Tracking), ERP Schedule integration, Historian, TrakSYS-enabled IIoT Smart Devices, and Maintenance Management.
Challenges
The core issues that Milo’s Tea was facing were all related to a lack of real-time data, insight, and communication.
- Manual recording of data was unreliably accurate and untimely
- Real-time actionable information was not readily available
- The organization lacked visibility into how production was performing
- Siloed data truncated informed decision-making
Goals
Traditional MOM solutions for digitally transforming factories were expensive and cumbersome compared to modern technologies. The equipment and infrastructure that was typically required had a large footprint and often needed significant production downtime to implement and test. To make matters worse, traditional MOM systems were not guaranteed to facilitate interoperability. The infrastructure that was meant to tie things together would end up creating yet another barrier to entry for manufacturers who sought to connect their factories digitally. That’s where TrakSYS (and the TrakSYS-enabled Smart Devices) came in.
To deliver the desired results as efficiently and effectively as possible, Polytron implemented a balanced approach of automatic data collection from most of the machine PLCs and TrakSYS-Powered Smart Devices in areas where PLCs did not exist. These Smart Devices (consisting of only a palm-sized coordinator and data collector) would seamlessly integrate into the existing system architecture at Milo’s Tea. They would provide real-time data and feedback with a minimal footprint, no production disruption, and did not necessitate infrastructure updates.
Utilizing TrakSYS in conjunction with the native Smart Devices, Polytron sought to:
- Increase production throughput
- Provide real-time actionable information to drive manufacturing improvements
- Provide manufacturing visibility throughout the organization
- Provide a platform for digital transformation that supports enterprise growth
- Integrate data from multiple systems to provide a single source of truth
- Migrate legacy data silo applications into the new platform
Solution Overview
TrakSYS was (and continues to be) the MOM platform that helped integrate, aggregate, contextualize, display, and report actionable insights. Multiple solutions were implemented using the TrakSYS platform over a two-year period. Each phase delivered an ROI that helped fuel the subsequent phase.
- Performance Management for three filling lines with automatic data collection from 10+ PLCs. The system was configured to capture machine states, production/reject counts, and the first fault for each machine.
- Sage ERP Integration for downloading production schedules automatically into TrakSYS.
- TrakSYS IIoT Smart Devices implemented in Empty Bottle Area to count bottles where no PLC existed.
- Performance Management for Line 4 and extension of data collection to additional machines.
- TrakSYS Historian for process and packaging time-based data analysis.
- TrakSYS Maintenance Management was implemented to replace a legacy point solution that acted in a siloed fashion, was unintuitive, and had long since grown obsolete.
- Rollout to the second factory with all of the functionality listed above.
- Scoreboards across many Machine Centers for real-time shift performance.
- Future Phases: Milo’s Tea is evaluating using TrakSYS for Warehouse Management, Quality Management with SPC, Finite Scheduling, Visual Workflow and expanding TrakSYS to all of the manufacturing assets in both facilities.
Solution Features
- Automatic data collection from Machine PLCs to identify stoppage reason, machine state and production/reject counts
- IIoT Smart Devices for areas in manufacturing that do not have PLCs
- Extensible functionality within TrakSYS to support Milo’s Tea specific requirements
- A platform that supports:
- Multiple MOM functions
- Expansion into Industry 4.0 advanced solutions
- Enterprise visibility
- Business digital transformation
Key TrakSYS Features
- IIot Smart Data Collectors
- Historian
- Performance Management
- Journals
- Tasks
- Maintenance Management
- Material Management
- DMS / ERP Integration
Results
Utilizing real-time production data to optimize manufacturing, the Milo’s Tea team recouped the initial project’s costs within three months. With their newly acquired real-time insights, intuitive TrakSYS user interface screens, dashboards, and reports, the plant floor departments were able to rapidly communicate, share knowledge, and resolve production roadblocks. Making use of these tools resulted in an OEE increase from 51% to 79% after the initial implementation. Actual OEE has increased by 55%, which translates directly to 55% more cases shipped using the same assets and personnel. Additionally, teams are now financially incentivized to continually meet and exceed daily line OEE goals, which currently sit at 80%.
“Utilizing the maintenance components of TrakSYS has enabled our teams to get a better hold on predictive and preventative maintenance intervals, tasks and practices. As our TrakSYS implementation evolves, we plan on incorporating our maintenance solution into other areas of production to help facilitate interdepartmental communication and production optimization.” Scott McDaniel, Manager of Information Systems
“TrakSYS also helped Milo’s Tea get a handle on bottle scrap,” notes McDaniel. “There was a very visible scrap issue that needed addressing. Large bags filled with unknown numbers of unused bottles were thrown out daily. By utilizing the TrakSYS Smart Devices, we were finally able to account for scrapped bottles, both those with labels, and those without. Smart Devices were placed at the start of all four lines: before the labeler, at the exit to the bottle room/entrance to the filler room, and at the start of the performance system. We began using these metrics as our scrap number in accounting monthly write-offs.”
TrakSYS also enabled the Milo’s Tea team to plan for the future. With its modular nature and seamless extensibility, TrakSYS will grow with them, and allow for expansion into other functional areas and multi-site deployments.
- Measurable ROI across all phases including 3-month payback on Phase 1
- Increased output at Factory One enabled construction of the second factory to be postponed by 18 months
- Platform for rapid and cost-effective deployment of any new requirements
Dashboards
Maintenance Weekly Overview
Maintenance dashboards give supervisors a quick view of key metrics for the current week. These include graphs showing availability losses, technician hours by priority, and recently completed work orders.
Filler Score Board
This dashboard is presented on a large monitor above the fillers. Operators can see their shift uptime, current and last hour production rates, and product targets. An image of the product currently in production is displayed for easy identification.
Plant Overview
Overview dashboards are displayed on large monitors throughout the plant and in offices. Teams can quickly and easily identify the status of each production line in the plant. The information displayed for each line includes the current production order, the filler rate, line status, and the OEE for the current shift and day.
About Parsec
Utilizing their 30 years of experience in manufacturing, Parsec created TrakSYS™: a best-in-class operations management software application and solution platform designed to significantly improve manufacturing operations. TrakSYS aggregates data from multiple sources to deliver real-time, actionable intelligence that helps manufacturers to reduce production costs, decrease lead time, and improve profitability. TrakSYS is deployed at thousands of factories, in over 100 different countries.
Credit: Source link