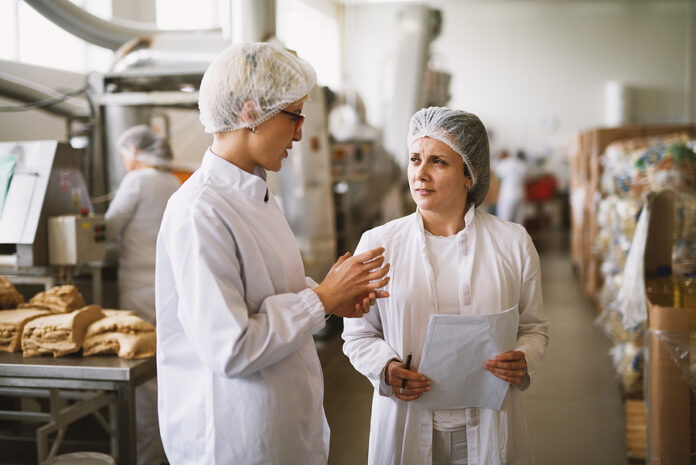
Although nine in 10 food manufacturing companies believe they understand what it takes to build and sustain a strong food safety culture, only 27% report that their employees consistently follow established protocols, according to the results of Intertek Alchemy’s 2024 Survey of Frontline Employee Training Programs.
This leaves a startling 73% of companies with employees who don’t always adhere to protocols, despite training efforts. The most common reason cited for this non-compliance is employees’ preference for doing things “the old way” (57%), followed by employee disengagement (34%) and a lack of severe consequences (34%).
To help companies improve employee performance, the research highlights several best practices for workplace training:
- Additional training hours: A mere 30% of frontline workers receive more than 20 hours of additional training per year beyond new hire onboarding. Companies that provide 20+ hours of additional training each year improve employee motivation by 13%. And motivated employees are three times more likely to follow established procedures.
- Professional development: The majority (84%) of companies provide refresher training to frontline workers, but only 38% of workers receive professional development training. Companies that have a mature professional development program are 119% more likely to see a positive impact on employee retention.
- Accurate worker instruction: Most facilities provide on-the-job supervisor coaching (73%) and peer-to-peer training (62%), but 22% of companies report that employees pass along misinformation to their peers. However, companies that integrate cross-functional team members into their learning management or training teams have a 58% higher likelihood of accurate worker-to-worker instruction.
- Reinforcement programs: Team meetings (78%) and coaching from team leaders (67%) are the most common methods for reinforcing training. Companies that have a strong training reinforcement program are three times more likely to have employees consistently following standard operating procedures.
- Training documentation: Only 31% of food manufacturing companies use a learning management system (LMS) to document and manage employee training records. It’s more common for companies to rely on paper-based documentation (33%) or spreadsheets (33%). Using an LMS could improve the accuracy of training data and make it easier to access and track.
- Site-specific training examples: Nearly all companies (92%) that have made it a practice to use site-specific examples from their own facility in training materials say their employees are successfully able to recognize and prevent potential problems on the floor.
For more insights, download the full report.
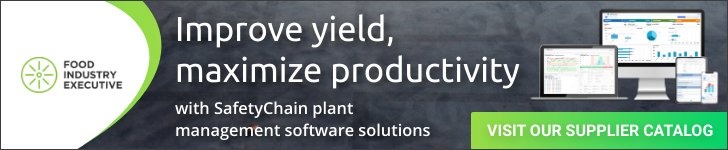
Credit: Source link