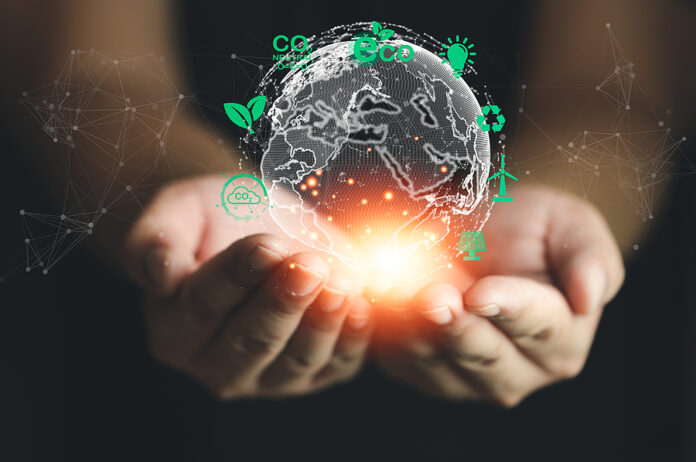
By Matt Roman, Director at ENGIE Impact
Key Takeaways:
- The food industry contributes to 26% of global greenhouse gas emissions, necessitating urgent action to meet climate targets.
- The Department of Energy (DOE) is investing billions in clean energy technologies, providing crucial support for the food manufacturing sector to implement Net Zero strategies.
- Effective decarbonization requires cross-functional collaboration, tailored strategies, and robust data collection to guide investments and achieve long-term sustainability goals.
Climate change and its impact on the planet continue to be apparent around the globe. As noted by the Paris Agreement, in order to limit global warming to 1.5°C, greenhouse gas (GHG) emissions must peak by 2025 and decline more than 43% by the year 2030. Such ambitious targets will require both the public and private sectors to commit to taking a closer look at their operations to identify ways to limit their emissions, and the food industry is no exception.
The reality is that the food industry is responsible for 26% of global greenhouse gas emissions, and manufacturing is one element of the food lifecycle that can’t be ignored. Fortunately, more federal and state funding is emerging to support energy-intensive industries including food and beverage. Just recently, the Department of Energy (DOE) launched the Industrial Demonstrations Program (IDP), which has awarded more than $6.3 billion in investments for technologies to support the implementation of clean energy projects, including those in the food manufacturing sector. As food manufacturing professionals begin to plan for their Net Zero strategies, and look to new opportunities to secure federal or state funding, preparing high-level decarbonization plans will be necessary. Generating a roadmap is crucial to successfully implement the strategies, technologies, and efficiencies needed to work towards emissions reduction targets.
While there are many inhibitors to implementing decarbonization efforts, new technology is helping manufacturing professionals gather the data they need to assess and plan for initiatives that actually pay off. But before operation managers can select and integrate the technologies, such as heat pumps, electric heaters, and solar photovoltaic systems, among others, they must approach decarbonization as a whole business transformation.
Take a holistic approach to avoid roadblocks
Having a holistic approach to corporate decarbonization ensures recognition of both the scale and breadth of the organizational effort that is required to successfully deliver long-term carbon-reduction outcomes. It’s not simply one role or department tasked with the undertaking, or a project with a start and end date. For food and beverage brands in particular, with multiple manufacturing sites and distribution centers across various regions, the approach must be a cross-functional effort that brings multiple teams together. In doing so, food manufacturers can prioritize their focus, obtain effective internal governance, identify additional finance options, and better integrate decarbonization data.
Prioritize factory data to identify the best levers
To identify where to invest time and funds, food manufacturers must secure data to capture their baseline emissions and energy use. This should be both at the plant level as well as within specific key manufacturing lines or processes. With this starting point data in hand, projections can be made for what business-as-usual looks like and will continue to look in five, 10, or 15 years from now. If no significant changes are made, this baseline data can account for what costs and output should be anticipated. Without it, manufacturers are blindly investing in and selecting the technologies and tools to effectively reduce emissions.
Baseline data also supports the creation of “digital twins” to better project where the business wants to be with its emission reduction targets. Creating a digital twin of the manufacturing plant allows teams to identify the right levers needed to close the gap from business today to Net Zero. These digital projections can be compared against the cost of operation, carbon emissions, and payback period. This early approach to data collection helps the entire organization adopt the mindset of decarbonization as an ongoing activity vs. divided projects.
Data brings scalability, but avoid cookie cutter plans
In gathering baseline data, food and beverage manufacturers may be tempted to seek out one decarbonization plan to roll-out at each of their manufacturing and distribution sites. Yet cookie cutter Net Zero plans don’t provide the necessary level of detail required to bring impactful results. Manufacturing plants’ operational data will vary based on the facility size, the location and local temperature, and the configuration of equipment. The reality is that each operating site is unique, and small details such as when to replace a gas boiler with a heat pump and the specific size needed, will vary at each plant. Cross-functional coordination and base-line data will alleviate the hurdles when planning for decarbonization roadmaps at scale. Yet, baseline data can still bring efficiency, and the principles and practices identified at one plant can be more easily assessed for viability in another.
Food manufacturers shouldn’t approach decarbonization efforts with intimidation. Embarking on Net Zero strategies with a holistic approach will require collaboration from organizational leaders at every level, from finance, technology, operations, procurement, to sales and marketing. It requires a true collaboration in order to understand not only the current state of decarbonization at the business, but what success will ultimately look like. These early initiatives provide a strong foundation that will allow organizations to maintain progress and meet, or exceed, Net Zero targets.
Matt Roman, Director at ENGIE Impact, has more than 25 years of experience in corporate energy management and sustainability strategy, industrial equipment energy optimization, plant engineering, construction project management, and corporate sustainability metric creation and reporting.
Credit: Source link