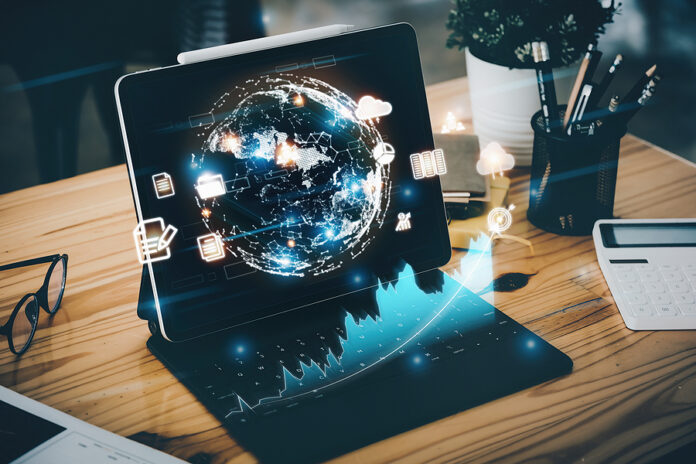
Key Takeaways:
- Successful digital transformation requires a foundation of careful assessment and planning, starting with an honest evaluation of current technological maturity and organizational readiness before implementing any new systems.
- The transformation should be built around core technology pillars while following a phased implementation approach that maintains production continuity and addresses both technical integration and cultural change management.
- Measuring transformation success requires tracking multiple interconnected metrics across operational, financial, and quality dimensions, while ensuring systems are scalable and adaptable for future growth.
Digital transformation in food manufacturing isn’t just about implementing new technology — it’s about fundamentally reimagining how your organization operates in an increasingly digital world. For food manufacturers, the stakes are high, as they have to balance innovation with food safety, regulatory compliance, and operational efficiency.
Success in this complex environment requires a methodical approach that starts with an honest self-assessment.
Understanding your starting point
Before starting any transformation projects, it’s important to figure out where your company stands in terms of technology. This means taking a close look at your existing manufacturing systems, processes, and capabilities across your manufacturing operations.
Start by documenting your current technology stack, including:
Beyond the technical assessment, evaluate your organizational readiness. What’s the level of digital literacy on your team? Will they require upskilling? Can you identify potential champions for change and areas of resistance? Compare your current state against industry benchmarks to identify gaps and opportunities.
Building your strategic framework
Successful digital transformation requires clear objectives aligned with business goals. Your roadmap should address specific challenges while supporting broader organizational strategies.
Here are several potential goals to consider when developing your strategy.
Operational efficiency:
- Target overall equipment effectiveness (OEE) improvements of 15-20%
- Reduce downtime through predictive maintenance
- Optimize resource utilization across production lines
- Streamline changeover processes
Quality management:
- Implement real-time quality monitoring
- Reduce quality defects by 50%
- Enhance traceability capabilities
- Automate compliance documentation
Sustainability goals:
- Reduce energy consumption by 25%
- Optimize water usage in processing
- Minimize waste through improved production planning
- Track and report environmental metrics
Identifying core technology pillars
Your transformation roadmap should be built around key technology pillars that support your strategic objectives. These pillars may include the following.
Manufacturing execution systems (MES)
Modern MES platforms serve as the backbone of digital transformation, providing real-time visibility into production operations. These comprehensive systems deliver essential capabilities including production scheduling optimization to maximize throughput, real-time performance monitoring across all production lines, seamless quality management integration for ensuring product consistency, and robust maintenance planning capabilities that help prevent costly downtime.
By centralizing these critical functions in a single platform, MES solutions create a unified operational view that enables data-driven decision making and continuous process improvement across the entire manufacturing operation.
Industrial Internet of Things (IIoT)
IIoT sensors and connectivity form the nervous system of modern food manufacturing operations, enabling comprehensive data collection across your entire facility. These systems continuously monitor equipment performance, track environmental conditions throughout your production areas, measure energy consumption at both machine and facility levels, and capture critical product quality parameters in real-time.
This network of connected sensors creates a continuous stream of actionable data that drives improvement in efficiency, quality, and resource use while providing the foundation for predictive analytics and automated decision-making capabilities.
Advanced analytics
Advanced analytics capabilities transform the vast amount of collected data into actionable insights that drive operational excellence. By leveraging sophisticated predictive maintenance algorithms, manufacturers can anticipate and prevent equipment failures before they impact production.
- Quality trend analysis reveals subtle patterns that might otherwise go unnoticed, enabling proactive interventions to maintain product consistency.
- Production optimization models continuously analyze and adjust parameters to maximize throughput while minimizing waste.
- Detailed resource utilization patterns highlight opportunities for improved efficiency across labor, materials, and energy usage.
Together, these analytical tools enable a shift from reactive to proactive management of manufacturing operations, driving continuous improvement across all aspects of production.
Developing an implementation strategy
Successful implementation requires a carefully phased approach that maintains production continuity while driving transformation.
Here’s an example of how this approach might look over a year-long period.
Phase 1: Foundation building (months 1-3):
- Establish digital infrastructure
- Implement core MES functionality
- Deploy initial IoT sensors
- Begin data collection
Phase 2: Process optimization (months 4-8):
- Integrate quality management systems
- Implement predictive maintenance
- Deploy advanced analytics
- Enhance automation capabilities
Phase 3: Advanced capabilities (months 9-12):
- Enable AI-driven optimization
- Implement advanced scheduling
- Deploy digital twin capabilities
- Enhance supply chain integration
Managing change management
If you’re already on your digital transformation journey, you know technology implementation is only half the battle — success hinges as much on people as it does on technology.
Effective change management requires a coordinated approach across multiple organizational dimensions. Start by establishing a clear governance structure with well-defined roles and responsibilities, ensuring leadership alignment at all levels. This foundation enables consistent communication and sets clear performance expectations throughout the organization.
At the heart of successful transformation is a comprehensive training and development program that addresses both technical and cultural aspects of change. Begin with a thorough assessment of skill gaps across your workforce, then develop targeted training programs that build both technical competency and confidence. Standard operating procedures should be created and regularly updated to reflect new digital workflows, while knowledge-sharing mechanisms ensure best practices spread throughout the organization.
Perhaps most importantly, digital transformation requires fundamental cultural change within the organization. Foster a data-driven decision-making environment where teams are encouraged to experiment and innovate within appropriate boundaries. Create mechanisms for recognizing and rewarding early adopters and those who champion new digital processes. Establish clear feedback channels that allow employees to share challenges and suggestions, creating a continuous improvement loop that strengthens the transformation process. This cultural shift, supported by strong leadership and comprehensive training, creates the foundation for sustainable digital transformation that extends well beyond the initial implementation phase.
Measuring success
A clear set of metrics that covers multiple areas of operation will help track the success of digital transformation initiatives.
From an operational perspective, key indicators may include:
- Overall equipment effectiveness (OEE) to measure equipment performance
- Quantifiable reductions in production downtime
- Improvements in production throughput
- Gains in energy efficiency across facilities
These operational metrics directly influence the financial measures that demonstrate transformation value, including:
- Return on investment calculations
- Documented cost savings across various operational areas
- Direct revenue impact from improved capabilities
- Measurable productivity improvements that affect the bottom line
Quality metrics round out the measurement framework, encompassing critical factors such as:
- Defect reduction rates
- Improvements in first-pass yield
- Strengthened compliance rates across regulatory requirements
- Reductions in customer complaints
Together, these interconnected metrics provide a holistic view of transformation progress and help justify continued investment in digital initiatives.
Future-proofing your investment
To get the most out of your technology for years to come, ensure your digital transformation roadmap includes provisions for both scalability and continuous improvement. Design systems that accommodate future growth, enable seamless multi-site deployment, and plan for capacity increases as demand grows. Technology infrastructure should be flexible enough to evolve with advancing capabilities, while teams continuously monitor emerging technologies and test new features that could deliver additional value.
Regular evaluation of potential upgrade paths and strong maintenance of vendor relationships ensure your transformation investment continues to deliver value well into the future, adapting to changing business needs and technological innovations.
And remember that digital transformation is a journey, not a destination. Your roadmap should also be flexible enough to adapt to changing business needs while maintaining focus on core objectives. Success requires commitment from leadership, engagement from employees, and a clear vision of the future state you’re working to achieve.
By following this structured approach to digital transformation, food manufacturers can drive significant improvements in efficiency, quality, and sustainability while positioning themselves for future success in an increasingly digital world.
Further Reading:
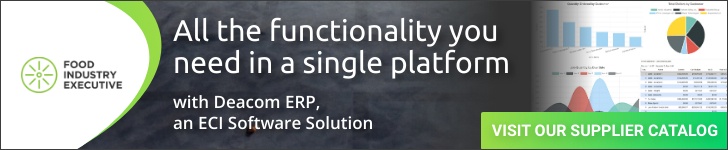
Credit: Source link