
Key takeaways:
- Equipment is aging (24-year average) and labor shortages are driving higher breakdown costs, according to a new report from MaintainX.
- Most teams (58%) remain trapped in reactive maintenance despite aiming for preventive strategies.
- Successful cost-reduction comes from implementing EAM systems, inventory management improvements, and AI solutions (44% already using/piloting).
On paper, current maintenance strategies look forward-thinking and proactive. In practice, most teams remain trapped in endless cycles of breakdown and repair. Equipment is aging, experienced technicians are retiring, and while technology offers promising solutions, implementation lags behind.
MaintainX’s recent survey of 1,320 maintenance professionals found that while maintenance teams are successfully reducing downtime incidents — 74% of respondents reported stable or decreased downtime — costs are spiraling when failures do occur — 31% of facilities experienced rising downtime costs.
There are three main factors driving this cost acceleration:
- Aging equipment: Fixed assets have reached an average age of 24 years.
- Rising costs: Supply chain disruptions continue to drive cost increases in replacement parts.
- Technical labor shortages: There is a diminishing pool of experienced maintenance specialists, and wages for such roles are increasing.
Roughly seven in 10 respondents identified preventive maintenance as a core strategy, but fewer than 35% dedicate most of their maintenance hours to it. Instead, 58% of teams continue allocating over half their time to reactive repairs — a particularly dangerous approach in food manufacturing where unplanned stoppages impact not just production targets but food safety compliance.
So what solutions are working?
Companies that have effectively reduced costs are investing in solutions like enterprise asset management (EAM) systems, improving parts and inventory management, and adopting Total Productive Maintenance (TPM) and Lean practices.
In addition, facilities that experienced higher-than-expected downtime were more than twice as likely (40% vs. 18%) to implement AI across multiple maintenance processes. Nearly two-thirds of respondents said they plan to deploy AI-powered maintenance solutions by 2026, and 44% have already adopted or piloted these technologies.
These solutions address dual challenges faced by food manufacturers — preserving institutional knowledge as experienced workers retire and transitioning from reactive firefighting to data-driven preventive strategies.
Find more maintenance insights in the full report.
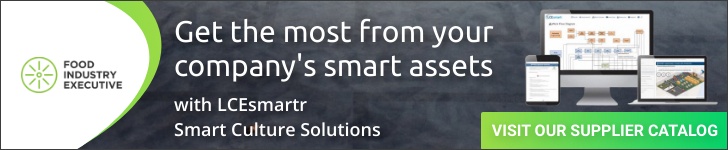
Credit: Source link