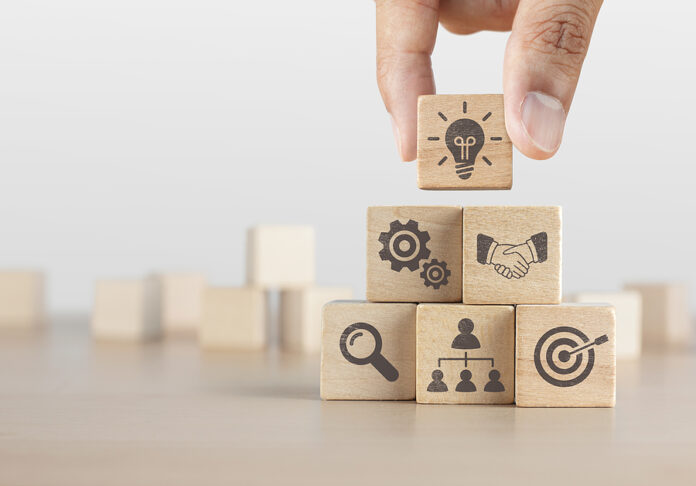
By John Robertson, Vice President, Food & Beverage and Consumer Packaged Goods, Life Cycle Engineering
Key Takeaways:
- The food and beverage industry faces major challenges including knowledge loss from retiring workers, difficulty attracting talent, supply chain disruptions, and maintaining food safety standards.
- Best practices for optimizing production include embracing reliability and lean manufacturing principles, implementing automation where possible, and investing in predictive maintenance technologies.
- Leadership plays a crucial role in operational excellence by empowering employees, investing in training and development, and driving innovation to stay competitive.
The food and beverage industry is always changing, with new challenges surfacing alongside the ones we’ve been dealing with for years. Whether it’s workforce engagement, optimizing production or ensuring the supply chain stays strong, the road to operational excellence can be tricky — but it’s worth it.
Let’s dive into some of the biggest hurdles and best practices that can help businesses run smoother, work smarter, and deliver top-notch products to consumers.
Pressing operational challenges in the food and beverage industry
The food and beverage industry is dealing with many operational challenges that can greatly impact productivity, quality, market share and the bottom line. Here are some of the big ones companies are facing:
- Human capital and legacy knowledge: One big issue is the aging workforce. As experienced workers retire, they take with them years of valuable knowledge. As newer generations join the workforce, closing this knowledge gap is crucial to keep operations running smoothly.
- Attracting new talent: Recruiting and retaining top talent is tough right now. The job market is competitive, and skilled workers are in high demand. Food and beverage companies need to create workplaces that stand out — think not only great pay and benefits, but investment in career growth, employee engagement, and flexibility in work hours — to attract the fresh faces needed.
- Culture of ownership: Operational excellence doesn’t happen unless everyone feels they own part of the process. Building a culture of empowerment and accountability is key. When people understand how their work impacts the bigger picture, they’re more likely to take the initiative and help the business to continue to move forward.
- Supply chain disruptions: Supply chain issues are still a massive headache. Whether it’s shortages of raw materials, delivery delays, or geopolitical challenges, these disruptions can seriously impact operations. Companies need to be ready with strategies to handle these challenges, like diversifying suppliers or investing in better tech to track progress real time to meet market demand.
- Food safety and quality: With increasing regulations focused on food safety, maintaining high standards are more important than ever. Failing to meet safety standards can result in costly recalls, damage to a brand’s reputation, and even legal trouble. Making sure food safety stays top-of-mind while optimizing production processes is a constant challenge in the industry.
These challenges are tough, but they also present opportunities for growth and improvement. Tackling them head-on can lead to smoother operations, better products, and a more substantial business overall.
Best practices for optimizing production processes
Getting your production processes dialed in to stay competitive in the fast-moving food and beverage industry is key. Here are some best practices that can help boost efficiency and keep things running smoothly:
- Embrace reliability and lean manufacturing: Reliability and lean manufacturing are all about operational stability, reducing waste and getting the most value from every step in the process. By streamlining operations, reducing downtime, and optimizing inventory management, manufacturers can not only ensure higher production rates but also trim unnecessary costs.
- Automate where you can: Automation leads to improvements in consistency, and safety. Packaging, labeling, and sorting can be automated, which lets your team focus on more complex tasks while ensuring minimal rate losses. Plus, fewer manual steps mean fewer chances for mistakes.
- Invest in predictive maintenance: Predictive maintenance uses sensors and data analysis to predict when machines are about to fail, allowing for proactive maintenance. This helps avoid unplanned downtime, lost production, and costly repairs, keeping everything running without interruptions.
By embracing these best practices, food and beverage manufacturers can improve efficiency and stay ahead of the curve in an increasingly competitive market.
The role of leadership in driving operational excellence
Leadership is critical to effectively and sustainably deploy operational excellence. Effective leaders set the tone for a culture of continuous improvement by:
- Empowering employees: Leaders who actively engage with the workforce, foster a culture of trust and collaboration encouraging employees to take ownership of their roles, leading to improved work-life balance that results in employee retention, higher productivity, improved regulatory compliance, and improved profitability.
- Investing in training and development: Equipping employees with the right skills, knowledge, and tools helps them excel in their roles, improve efficiency, and drive operational success.
- Driving innovation: Strong leadership encourages the adoption of new technologies and practices, ensuring the company stays at the forefront of industry advancements.
Operational excellence is a game-changer in food and beverage manufacturing if you want to stay ahead of the competition. Companies can boost efficiency, enhance product quality, and improve their overall performance by increasing employee engagement and embracing new technologies. But it’s not just about the tech — strong leadership, a resilient supply chain, and investing in your team’s growth are key to long-term success. When operational excellence becomes part of your company’s DNA, you have happy team members, better products, satisfied customers, and a healthier bottom line.
John Robertson serves as Vice President of Life Cycle Engineering’s Reliability Consulting Group, primarily responsible for predictable and sustainable business growth. His career encompasses over 35 years of manufacturing, consulting, and business leadership.
Credit: Source link