
The clock has officially run out on the FDA’s phase-out of PFAS (per- and polyfluoroalkyl substances) in certain food packaging applications. As legal pressure builds against top food brands, food manufacturing leaders must act swiftly to mitigate both regulatory and litigation risks.
The FDA’s PFAS deadline has passed: Final phase-out is here
On January 6, 2025, the U.S. Food and Drug Administration declared that 35 Food Contact Notifications (FCNs) for PFAS-based grease-proofing agents in paper food packaging are no longer effective. This marks the end of a voluntary phase-out process that began in 2020, when manufacturers agreed to stop selling these substances.
While the decision went into effect in January, the FDA allowed manufacturers to use existing inventory through June 30, 2025. That grace period has now expired.
Key implications for manufacturers:
- PFAS-coated wrappers, liners, and boxes are no longer authorized for use in food contact materials.
- The FDA is actively monitoring compliance with new analytical testing methods.
- Non-compliant companies may face regulatory action or be forced to issue recalls.
Hershey lawsuit signals legal risks for food brands
While regulatory enforcement increases, litigation risks are already unfolding. As of July 2025, Hershey’s is facing lawsuits alleging that PFAS were present in its food packaging — specifically in chocolate bar wrappers.
Highlights from the lawsuit:
- Plaintiffs argue the presence of PFAS makes Hershey’s products “misbranded” or “adulterated” under federal law.
- Claims include economic damages based on consumer deception and health risks.
- The case sets a precedent for how PFAS contamination — intentional or not — can expose companies to class action lawsuits.
This lawsuit underscores a broader industry challenge: even trace amounts of PFAS — migrating from packaging — can fuel legal claims tied to safety, misrepresentation, and consumer harm.
Four critical action steps for food manufacturers using PFAS
With both legal and regulatory threats in play, food companies must move decisively to eliminate PFAS risk across their supply chains.
1. Audit all packaging and ingredients
- Conduct a comprehensive audit of all food-contact materials, especially paperboard and liners.
- Request updated certifications or declarations from all packaging suppliers regarding PFAS content.
2. Eliminate PFAS from all operations
- Discontinue any use of legacy packaging with grease-proof coatings containing PFAS.
- Replace with verified PFAS-free alternatives, including bio-based coatings or recyclable films.
3. Build a paper trail of compliance
- Maintain supplier attestations, internal testing results, and third-party certifications.
- Use documentation to demonstrate a “reasonable certainty of no harm,” which is critical for both FDA compliance and legal defense.
4. Monitor legal and regulatory developments
- Track state-level PFAS bans — many of which are stricter than federal regulations.
- Establish a system to respond quickly to legal threats, including customer complaints, NGO scrutiny, or lawsuits.
Compliance is no longer optional
Between FDA deadlines and the expanding legal landscape, food manufacturers must take a proactive approach to PFAS:
- The regulatory window has closed as of June 30, 2025.
- Class action risks are real — and expanding beyond obvious use cases.
- Companies that take steps now to audit, replace, and document can better protect themselves from fines, recalls, and lawsuits.
In short, the industry has entered a new era of scrutiny around chemical safety in packaging. Those who act now to eliminate PFAS — and communicate that commitment — will not only reduce risk but gain a competitive edge in a transparency-driven market.
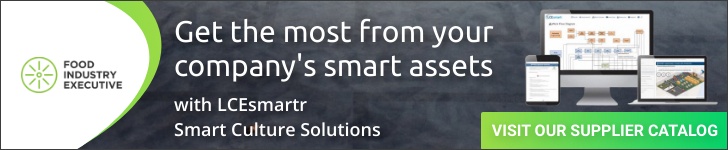
Credit: Source link